Testing Capabilities
Delta Specialty Coatings has a state of the art testing laboratory that has capabilities far beyond what's typical in the coatings industry. Here are some of the QC tests that we perform:
X-Ray Fluorescence (XRF): A non-destructive means of identifying metallic coatings and measuring thickness with extreme precision.
ASTM B568 describes the test procedure.
​
Deposit Stress Testing: An important but often overlooked test that helps us to control the stress of an electrodeposited coating is the bent fork stress tests. Stress tests should be done routinely at all plating shops, as a matter of "best practice".
​
Adhesion Verification: If your plating shop doesn't control the stress of their deposit with the test described above, their coatings may peel away from the substrate material. There are many other causes of poor adhesion, not the least of which is poor cleaning. Quantitative and qualitative tests should be performed to assure that a coating is properly bonded to the substrate.
Common tests for adhesion are ASTM D3359 (tape), ASTM B571 (burnish) and ASTM D4541 (bend).
​
​
​
Cyclic Voltammetric Stripping (CVS): Brighteners and grain refiners are important components of almost all plating baths. If their concentrations are not controlled, the coatings produced by the baths will have inconsistent physical properties.
Shown below is a crack in electroplated copper that could have been prevented if this plating shop had measured brightener and organic contamination using CVS.
​
​
Surface Tension: (I threw this in because I like to say "stalagmometer". Practice pronouncing it a few times, then say it at a party. People will think you're smart). A stalagmometer is an essential lab tool, especially for nickel and chrome platers. Among other things, good control of surface tension allows plating solutions to "wet" inside narrow recesses. If a part isn't wet, it doesn't plate.
​
Hull Cells: Most plating shops do a hull cell test now and then. But learning to interpret them takes many years of experience.
Knowledge of how to "read" hull cells is probably the most important skill that a plating lab tech can learn.
​
​
Resistance to Solvents: Delta applies many different types of organic coatings. To assure that a coating such as Xylan is going to perform as expected, we check for proper cure per ASTM D5402.
​
​
​
Wet Lab: All plating shops must perform titrations so they can calculate the necessary additions to their baths.

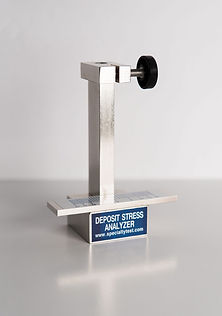
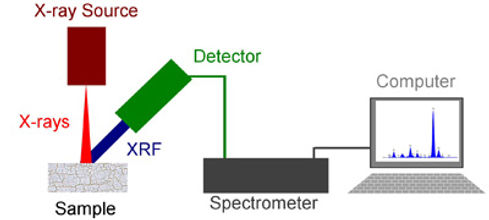





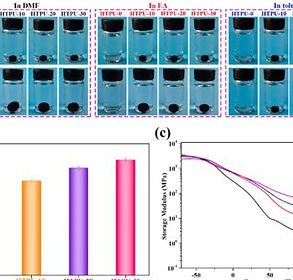
